Table of Contents
Introduction
In the ever-evolving landscape of aerospace engineering, it has emerged as a groundbreaking technology, revolutionizing how aircraft are designed, tested, and maintained. This transformative approach involves creating virtual replicas of physical objects, providing unprecedented precision and insight. In this article, we’ll dig into their role in aerospace, exploring real-world examples that showcase their impact on innovation and efficiency.
1. Understanding Digital Twins
Digital Twins refer to virtual replicas of physical objects or systems. In the context of aerospace, these are precise digital models of aircraft that mimic their behavior in the real world. The comprehensive representation of an aircraft in the digital realm enables engineers to simulate various scenarios, understand performance dynamics, and optimize designs before any physical prototype is created.
2. Designing Aircraft with Precision
Digital twins play a pivotal role in the design phase of aircraft. Engineers can create a virtual prototype that mirrors the physical aircraft, allowing for in-depth analysis and simulation. For instance, companies like Boeing and Airbus utilize digital twins to assess aerodynamics, structural integrity, and system interactions. This not only expedites the design process but also enhances the accuracy of the final product.
Virtual Prototyping
- It enables engineers to create a virtual prototype of the aircraft during the design phase.
- This virtual representation mirrors the physical aircraft, offering a detailed and accurate simulation.
Analysis and Simulation
- Engineers use this for in-depth analysis and simulation of various aspects of the aircraft.
- This includes assessing aerodynamics, structural integrity, and interactions within the aircraft’s systems.
Expediting the Design Process
- The usage of this expedites the design process by providing a comprehensive virtual environment for testing and refinement.
- Rapid simulations allow for quicker identification of design flaws and potential improvements.
3. Real-Time Monitoring for Enhanced Performance
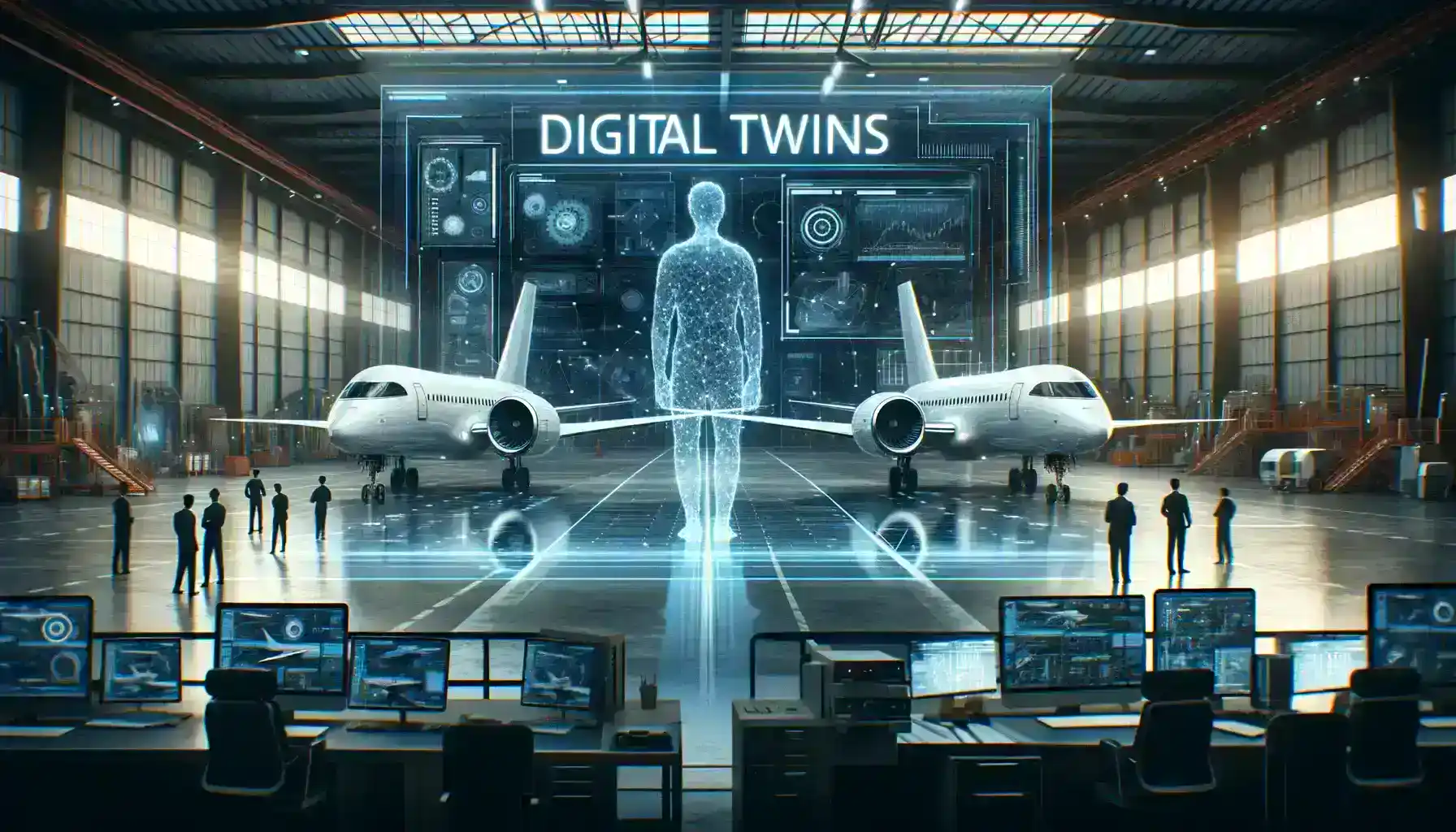
One of the key advantages of Digital Twins in aerospace is real-time monitoring. Aircraft generate an immense amount of data during flights, from engine performance to environmental conditions. By utilizing this, engineers can monitor this data in real-time, identifying potential issues and optimizing performance.
Rolls-Royce and Digital Twin Engines
Rolls-Royce, a prominent player in the aerospace industry, utilizes digital twins to monitor and optimize the performance of its aircraft engines. By collecting real-time data from sensors embedded in the engines, the digital twin provides insights into fuel efficiency, maintenance needs, and potential issues. This proactive approach has significantly reduced downtime and enhanced overall reliability.
NASA’s Digital Twin for Spacecraft
NASA employs such technology in the development and operation of spacecraft. The technology enables engineers to simulate various scenarios, predict potential challenges, and optimize mission parameters. This not only improves the success rate of space missions but also contributes to cost savings through more efficient planning.
4. Enhancing Maintenance and Predictive Analytics
One of the key advantages of such in aerospace is predictive maintenance. By continuously monitoring the aircraft’s performance through sensors and real-time data feeds, engineers can identify potential issues before they escalate. This proactive approach reduces unplanned downtime, lowers maintenance costs, and extends the lifespan of critical components.
Predictive Maintenance
- It enables continuous monitoring of an aircraft’s performance using sensors and real-time data feeds.
- This proactive approach involves predicting and addressing potential issues before they lead to downtime or failures.
Lufthansa Technik’s AVIATAR platform utilizes digital twin technology for predictive maintenance. The platform integrates real-time data from aircraft systems to identify and address potential issues, optimizing maintenance processes.
Continuous Monitoring with Sensors
- It integrates with sensors placed throughout the aircraft to collect real-time data on various parameters.
- These sensors monitor factors such as engine performance, system health, and overall operational metrics.
General Electric employs digital twins to monitor aircraft systems, including avionics and propulsion. Real-time analytics help predict component failures, allowing for timely maintenance and minimizing disruptions to airline operations.
5. Benefits of Digital Twins in Aerospace
Reduced Development Time
Boeing has implemented Digital Twins in the development of the 777X, their latest long-range, wide-body twin-engine jet. The use of Digital Twins allows Boeing engineers to simulate various design configurations and test performance under different conditions. This has significantly accelerated the development timeline, enabling them to identify and resolve potential issues in the digital realm before physical prototypes are built.
Cost Savings
General Electric (GE) employs Digital Twins in the development and manufacturing of the LEAP aircraft engine, a collaboration with Safran Aircraft Engines. The usage of such has streamlined the testing and optimization processes, reducing the need for extensive physical testing. This has led to substantial cost savings in the development phase, making the LEAP engine more cost-effective and competitive in the market.
Enhanced Safety
Embraer utilizes Digital Twins in the design and safety testing of their E-Jets E2 series. By simulating various flight conditions and scenarios in the digital environment, Embraer can proactively identify and address potential safety concerns. This meticulous approach to safety testing contributes to the high level of safety and reliability associated with the E-Jets E2 series before they enter commercial service.
Optimized Performance
Rolls-Royce’s Digital Twin technology is applied to the Trent XWB engine, which powers Airbus A350 XWB aircraft. Through detailed simulation and analysis, engineers can fine-tune the engine’s performance, optimizing factors such as aerodynamics and fuel efficiency. This not only ensures optimal performance but also contributes to fuel savings and environmental sustainability.
These concrete examples illustrate how leading aerospace companies leverage Digital Twins to achieve tangible benefits, including reduced development time, cost savings, enhanced safety, and optimized performance in their aircraft and engine programs.
6. Overcoming Challenges and Ensuring Security
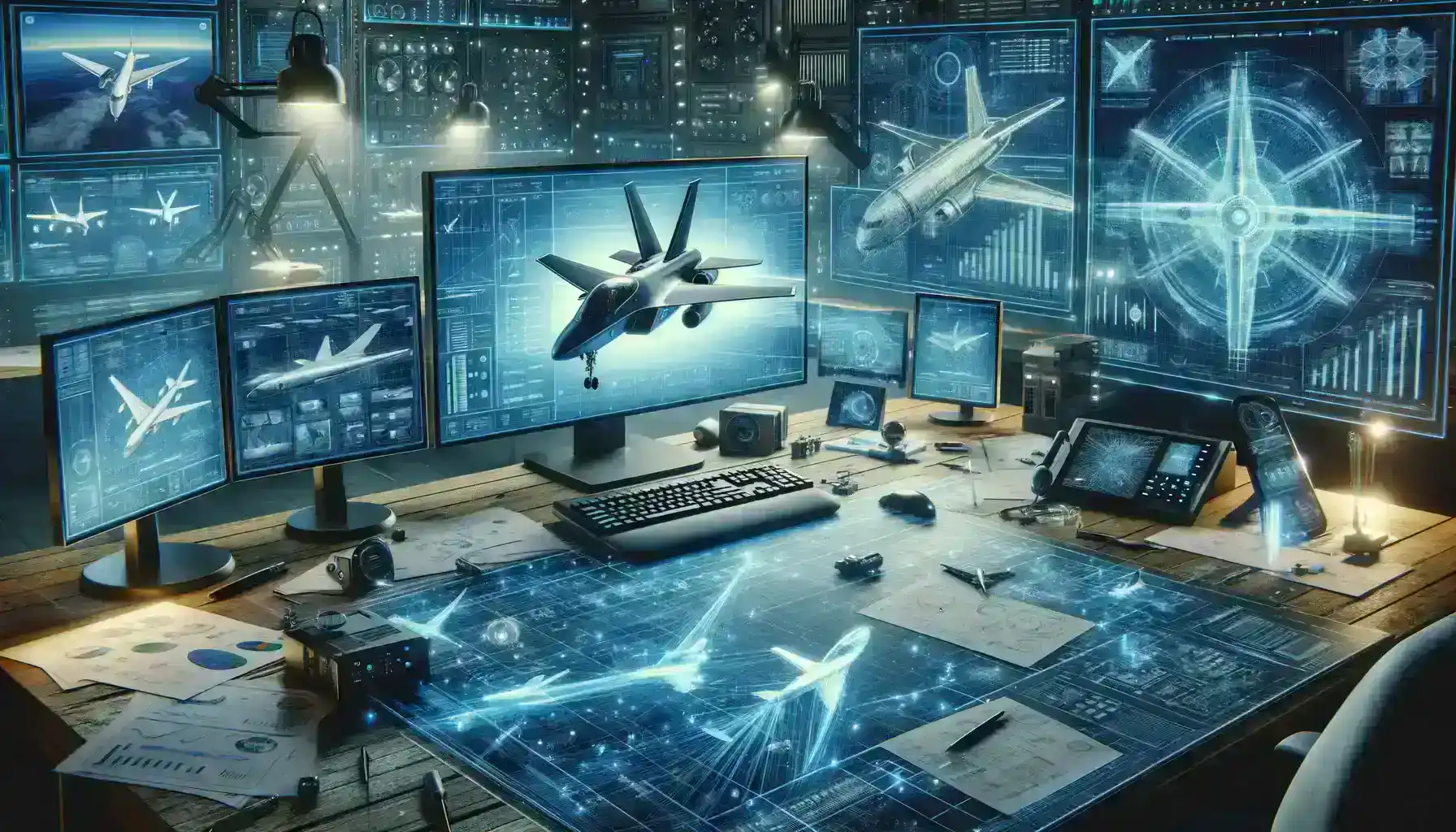
While such benefits in aerospace are substantial, challenges such as data security and privacy must be addressed. Ensuring the protection of sensitive data is paramount, especially considering the interconnected nature of digital twin technology. Aerospace companies are investing in robust cybersecurity measures to safeguard against potential threats.
Data Security Challenges
- It involves the collection and utilization of vast amounts of sensitive data related to aircraft design, performance, and maintenance.
- The interconnected nature of digital twin systems increases the risk of unauthorized access or data breaches.
Privacy Concerns
- Protecting the privacy of sensitive information, especially in a collaborative aerospace environment, is crucial.
- Stakeholders need to ensure that proprietary data and intellectual property are safeguarded.
Robust Cybersecurity Measures
- Aerospace companies are actively investing in robust cybersecurity measures to address potential threats to digital twin systems.
- This includes the implementation of encryption protocols, access controls, and secure authentication methods.
Data Encryption
- Encrypting sensitive data within digital twin systems ensures that even if unauthorized access occurs, the information remains unreadable and protected.
- Advanced encryption standards are employed to secure communication channels and data storage.
7. The Future Landscape
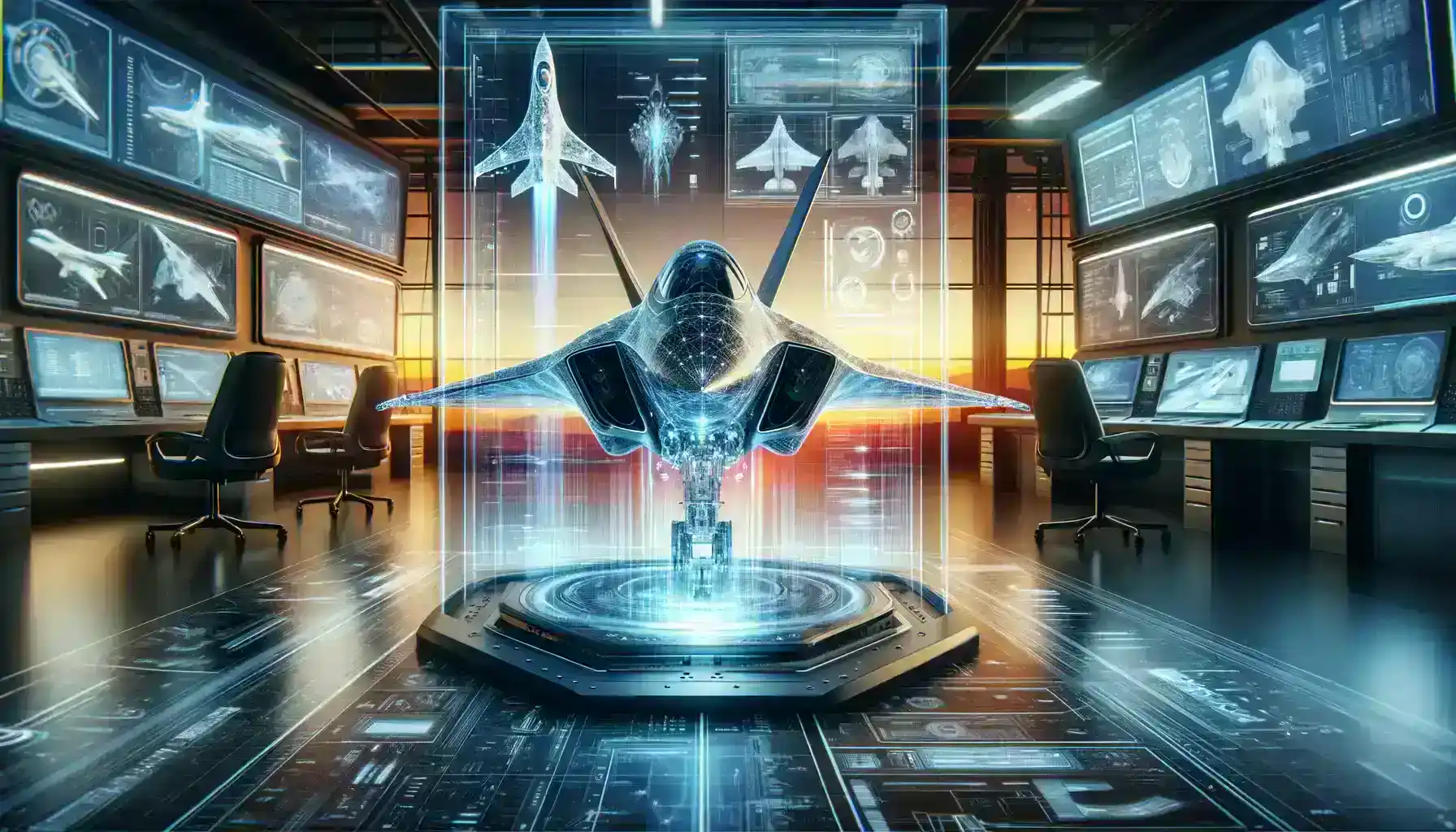
As technology continues to advance, the role of this in aerospace is poised to expand. The integration of artificial intelligence and machine learning will further enhance the predictive capabilities of digital twins, enabling even more precise analysis and decision-making. Additionally, collaborative efforts within the industry can lead to the development of standardized practices for such implementation.
Real-Time Anomaly Detection
- AI algorithms integrated into digital twins can continuously monitor real-time data for anomalies.
- This enables early detection of irregularities, contributing to improved safety and reliability of aircraft systems.
Pratt & Whitney, a leading aerospace manufacturer, is investing in AI-driven digital twins for its intelligent engine program. AI algorithms analyze real-time data to predict engine performance, optimize fuel efficiency, and reduce maintenance costs.
Collaborative Industry Efforts
- Collaborative efforts within the aerospace industry will drive the development of standardized practices for digital twin implementation.
- Shared frameworks and guidelines will facilitate interoperability and the seamless exchange of digital twin data across different aerospace platforms.
The Digital Twin Consortium is an industry association working to establish best practices and drive the adoption of digital twins across various sectors, including aerospace. Collaborative initiatives like this promote standardization and ensure a cohesive approach to digital twin implementation.
Integration with the Internet of Things (IoT)
- The integration of digital twins with IoT devices will enhance connectivity and data exchange capabilities.
- IoT sensors on aircraft components will provide real-time data, feeding into digital twins for comprehensive analysis and decision support.
Airbus is exploring IoT-enabled aircraft to improve operational efficiency and maintenance.
By integrating IoT sensors with digital twins, Airbus aims to create a holistic view of aircraft health, enabling proactive maintenance measures.
Human-Machine Collaboration
- Future digital twins in aerospace will likely involve increased collaboration between humans and machine intelligence.
- Human expertise combined with AI-driven insights will lead to more informed decision-making and innovative solutions.
Conclusion
Digital twins in aerospace represent a revolutionary shift in how the industry approaches the design, analysis, and maintenance of aircraft. The technology offers a real-time, in-depth understanding of aircraft behavior, impacting various facets of the aerospace sector. From streamlining design processes to enabling predictive maintenance, the applications of such are diverse and carry significant impact.
As aerospace companies increasingly adopt this technology, the benefits of precision and efficiency become apparent. The next generation of aircraft stands to gain substantially from the insights provided by digital twins, ensuring optimal performance and reliability.
The examples highlighted throughout this article, such as those from Boeing, Airbus, GE Aviation, and Pratt & Whitney, serve as compelling evidence of the transformative power of digital twins in shaping the future of aerospace engineering. As the industry continues to innovate and collaborate, it will play a pivotal role in elevating the standards of efficiency, safety, and overall excellence in aerospace technology.