Table of Contents
Industrial Automation is the center of a technological revolution changing the paradigm by which industries are produced, operated, and innovated. Picture a future of smart machines processing complex tasks, supply chains warning them of disruptions long before they occur, and factories operating with almost zero human error, a future made possible by today’s edge-of-the-impossible innovations. Automation is no longer just a trend—it’s an essential requirement, as a result of technological advancements, sustainability needs, and operational efficiency requirements.
According to MarketsandMarkets, growth of the global market will hit $395 billion by 2027 fuelled by the adoption of sophisticated technologies such as IoT, robots, and AI. In addition, McKinsey Company points out that industrial automation could result in up to 20% cost reduction in operations by achieving workflows that minimize operations and enhance decision-making.
In this article, we’ll explore 8 dynamic trends that are defining the trajectory of industrial automation, setting industries on a path of greater efficiency, adaptability, and innovation. Ready to explore the future of industrial innovation? Let’s dive in!
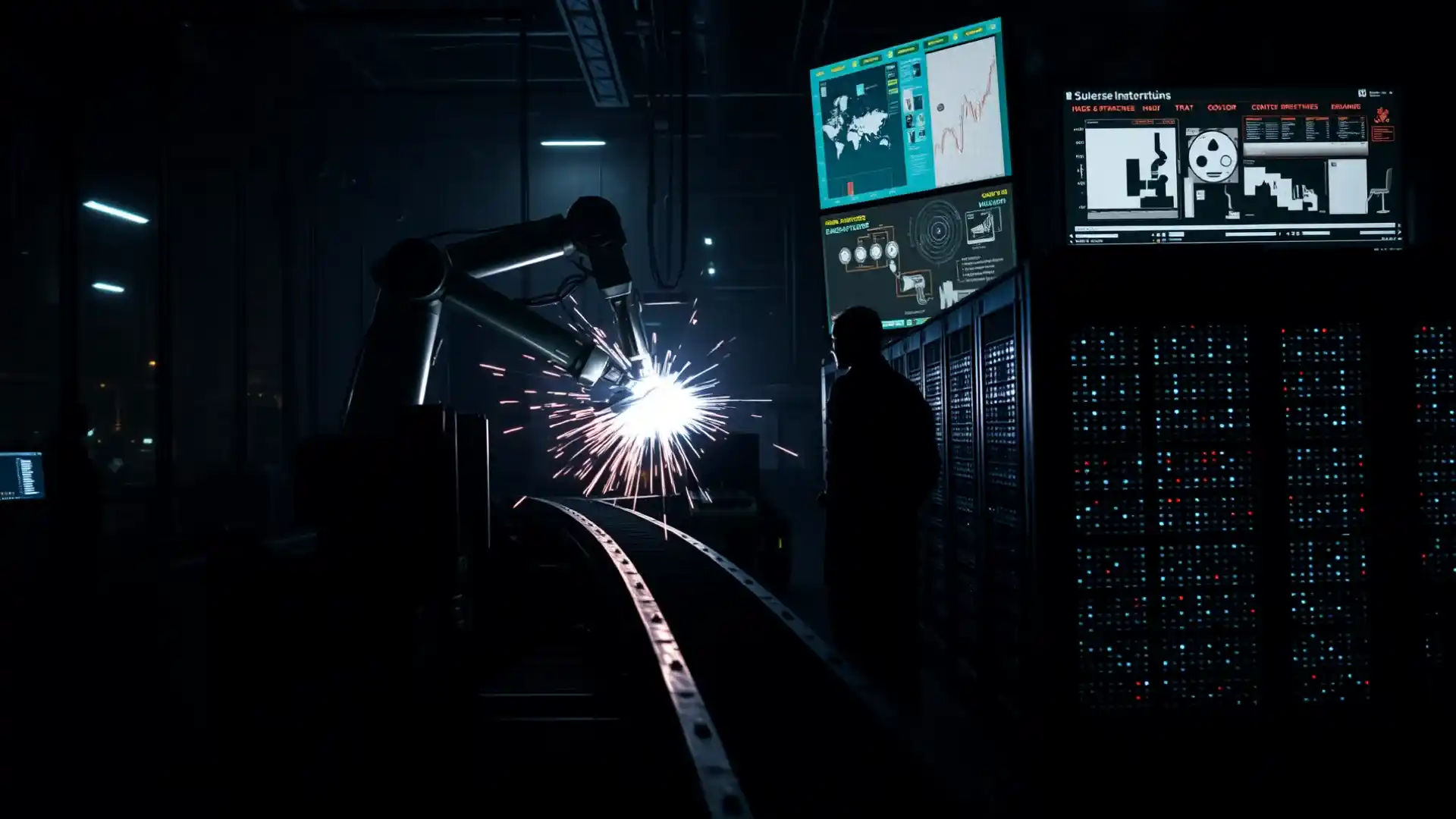
Industrial Automation Unveiled: What is It?
It refers to the application of emerging technologies such as AI, robotics, IoT, and machine learning for automation and optimization of industrial processes with limited human intervention. It does the substitution of monotonous manual work for automated systems, which leads to improvements in the quality of work, efficiency of work, and operational efficiency.
Through the use of smart machines and on-the-fly decision-making, it enables industries to anticipate their maintenance needs, react faster to changes, and optimize their workflows. It’s a transformative shift that’s driving industries like manufacturing, supply chain, healthcare, and energy toward innovation and adaptability.
Industrial automation is intelligent, faster, and more productive processes fuelled by technology.
The Power of Automation in the Industrial Sector
Industrial automation has been the engine behind current manufacturing, enabling businesses to reduce operational steps, increase efficiency, and raise levels of production. A PwC study on Industrial Automation reports that companies, that incorporate automation technologies, have productivity gains of up to 23% and simultaneously lower operational costs.
Using robotics, artificial intelligence, the Internet of Things (IoT), and intelligent technology, industries are maximizing their use of resources, minimizing expensive human mistakes, and ensuring consistent product quality. With this technological revolution, the way factories and production run is redefined, allowing corporations to gain a competitive advantage in today’s fast-changing global market.
Workplace safety has also benefitted significantly from automation. By eliminating the demand for human labor in hazardous and repetitive activities, companies have reduced the number of accidents and injuries, in turn providing a safer and more productive workplace for workers. The World Economic Forum highlights that industrial automation could potentially reduce workplace accidents by up to 30% by replacing workers in dangerous environments with machines.
In addition, a Deloitte report on smart factory trends found that 63% of manufacturing firms are currently using at least one type of automated technology to streamline supply chain flexibility and responsiveness, which supports industries in responding to a dynamically changing market environment.
Industrial automation is the driving force behind increased efficiency, productivity, and competitiveness. With technology continuing to move forward at a rapid pace, staying up-to-date with the latest trends in industrial automation becomes tougher and more important for manufacturers looking to maintain a competitive edge.
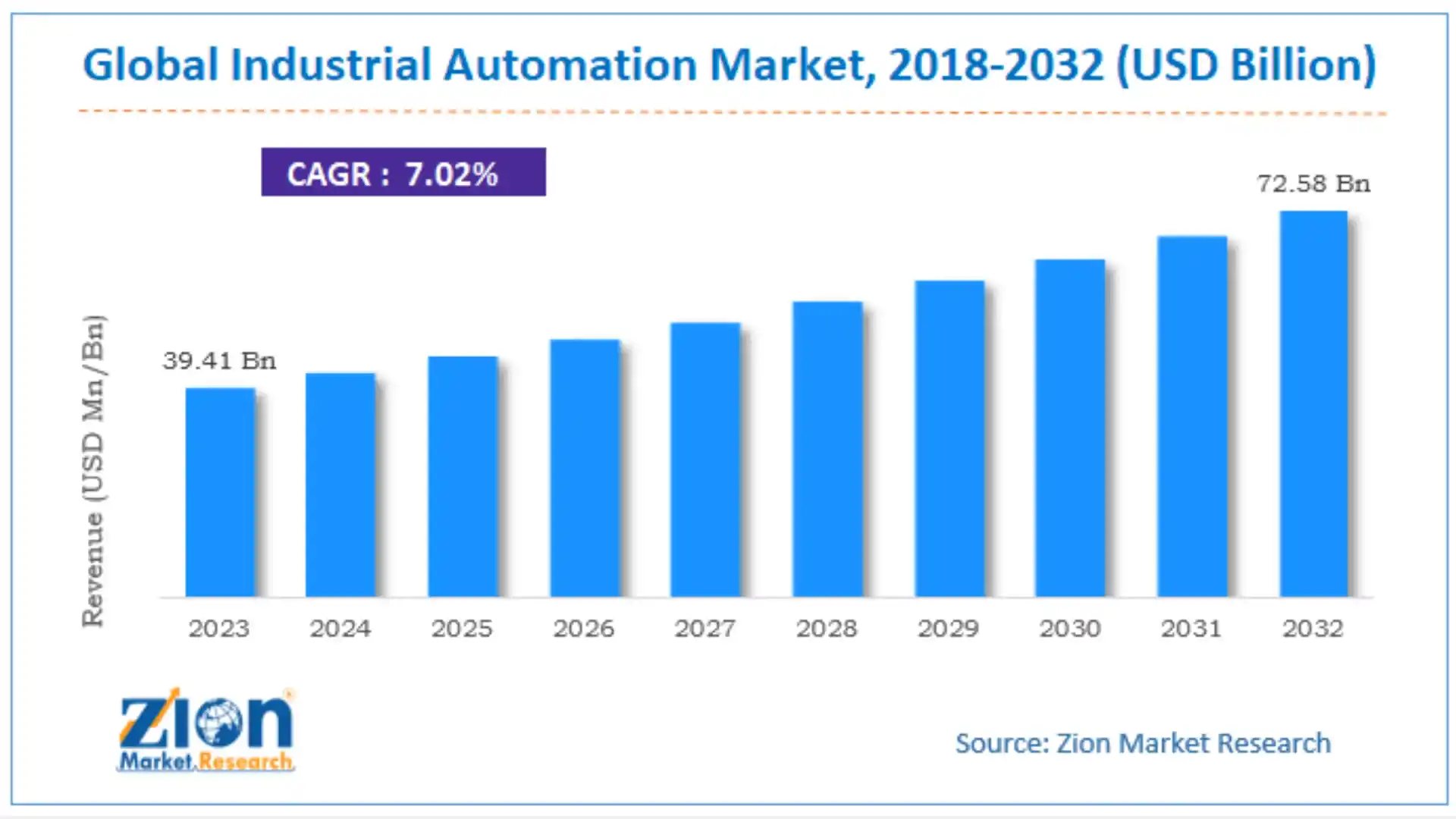
8 Dynamic Trends Shaping the Future of Industrial Automation
Some industrial automation trends have been around for several years but are still having a real impact on the world we work and live in. Other trends are more cutting-edge and just beginning to break into the conversation. Regardless of how new or proven the trend is, these trends are all real and relevant. Let’s have a quick overview of the top 8 trends in industrial automation that are reshaping the manufacturing industry as we close out 2024.
- AI-Powered Robotics Enhancing Precision & Efficiency
AI and robotics are at the forefront of the industrial automation transformation, offering new levels of speed, accuracy, and productivity. AI-enhanced robots can do complex manufacturing including electronics assembly, welding, painting, and packing-more quickly and accurately than is achievable by humans.
- Data Insight: As reported by PwC, 72% of companies aim to adopt AI-driven robotics in their business by 2025 and are seeing productivity gains of up to 30%.
- Impact on Industries: Among the applications for robotics, production lines in electronics, the automobile industry, and pharmaceuticals are currently being utilized to respectively streamline production cycles and reduce waste.
Such machines process massive data sets and dynamically respond to environmental disturbances on the production line minimizing errors, and downtime. They are a tool, complementing but not substituting labor so that human capital can be dedicated to high-level strategic planning rather than routine tasks.
- IoT Connectivity for Smarter Supply Chains
IoT enables industries to integrate devices and supply chain activities and provides real-time monitoring and intelligent predictive information. IoT-based sensors track inventories, surveil shipments, forecast maintenance needs, and even notify managers of problems long before they arise.
- Data Insight: A Deloitte study found that 63% of manufacturing firms are already utilizing IoT to improve supply chain flexibility, emphasizing its role in maintaining operational responsiveness to sudden market demands.
- Supply Chain Agility: IoT-based solutions enable companies to overcome the bottlenecks, identify the weaknesses, and rapidly adapt the supply chain networks to provide on-time delivery while remaining cost-effective.
IoT is enabling predictive ecosystems, providing the potential for supply chains to preempt disruptions, reduce the impact of disruptions, and react in real-time.
- Edge Computing Driving Faster Decision-Making
Edge computing is revolutionizing how industries process data. Compared to traditional centralized cloud computing, edge computing allows data processing in the source or even nearby—reducing the latency, enhancing security, and facilitating quick insights.
- Why It Matters: The ability to real-time data processing results in faster machine error responses (i.e. production stoppages being interrupted) and hence, allows operations to run consistently without any delay.
- Research Insight: Gartner estimates that by 2025, more than 75% of enterprises will adopt edge computing solutions to achieve AI and real-time services at reduced operational costs.
Edge computing, furthermore, will decrease the load on cloud networks and enhance the security of the cloud network by reducing the risk of external attacks.
- Collaborative Robots (Cobots) Redefining Human-Machine Interaction
Collaborative robots (cobots) are developed to work nearby in and cooperative fashion to humans, with the aim of increasing the productivity and safety of workers. Cobots carry out repetitive, dangerous processes, or very precise processes, relieve the workforce, and increase the production cycles.
- Data Insight: A Forrester report showed that industry applications of cobots are resulting in increases in productivity as high as 25%.
- Applications: Cobots are commonly employed in assembly lines, packaging, electronics, and logistics to automate manual tasks whilst improving ergonomics.
Cobots are designed with advanced sensors and safety features that enable them to adapt to the presence of workers, enhancing safety while reducing costly downtime. They represent a balance between innovation and human skill.
- Digital Twins for Predictive Maintenance & Operational Insights
Digital twins model real-world contexts to track machines, processes, or assets in order to provide companies with a predictive capability of failure and optimization of operations. These digital models open the door to allowing industries to experiment with scenarios, evaluate the change, and discover waste that does not require any physical change of the real world.
- Data Insight: According to Gartner, by 2025, 75% of companies will be using digital twin technologies to tackle predictive maintenance and enhance resource use.
- Maintenance Savings: The implementation of digital twins has allowed companies to decrease unplanned downtime by 20-30%, which in turn cuts costs and operational interruptions.
By far the most used is the technology in aeronautics, energies, manufacturing supply chain logistics, etc. They offer on-the-fly information about physical resources and their performance, from which data-based decisions can be made by the managers.
- Sustainability Through Green Manufacturing & Renewable Energy Integration
Sustainability remains the point of origin for technological progress in industrial automation. Advanced technologies such as AI, IoT, and automation are helping industries achieve their environmental goals by optimizing resource usage, minimizing waste, and integrating renewable energy sources.
- Research Insight: According to McKinsey, companies that use green automation solutions have reported carbon emissions reductions of 20-30% on average.
- Examples: Smart factories using AI can dynamically adjust energy consumption, reduce waste during production, and align themselves with international environmental goals, such as achieving carbon neutrality by 2050.
These advances are embedding green manufacturing at the heart of operational strategies, providing long-term sustainability whilst also improving profitability.
- Advanced Analytics & Machine Learning for Strategic Insights
Machine learning (ML) facilitates industries to interpret historical as well as currently streaming data to recognize patterns, forecast results, and control decision-making. This application of deep analytics provides industries with information to optimize processes, predict consumer demand, and avoid the expense of unscheduled downtime.
- Data Insight: According to the Boston Consulting Group, machine learning has the potential to improve manufacturing profitability by 20% by improving demand forecasting, production schedule optimization, and predictive analysis.
- Applications: Machine learning is applied in diverse fields such as predictive maintenance, market trend analysis, inventory optimization, and quality control.
Machine learning utilizes data to inform active decisions, transforming established processes into data-informed ones, and achieving quantifiable cost reductions and operational enhancements.
8. Cybersecurity & Resilience in the Age of Connected Devices
With the proliferation of the Internet of Things (IoT) and connected devices, cybersecurity has become a top operational priority. Automated networks are increasingly vulnerable to sophisticated hacking, leading to operational disruptions or data breaches.
- Data Insight: According to the World Economic Forum, a cybersecurity breach could paralyze up to 30% of supply chains by 2025 unless effective measures are introduced.
- Response: The security industry is deploying multi-stage approaches to cybersecurity, such as AI-assisted threat detection, high-level encryption, and intrusion detection and monitoring systems.
The security of automated systems guarantees stability in operations, prevention of injuries to the workers, and safeguarding of intellectual property.
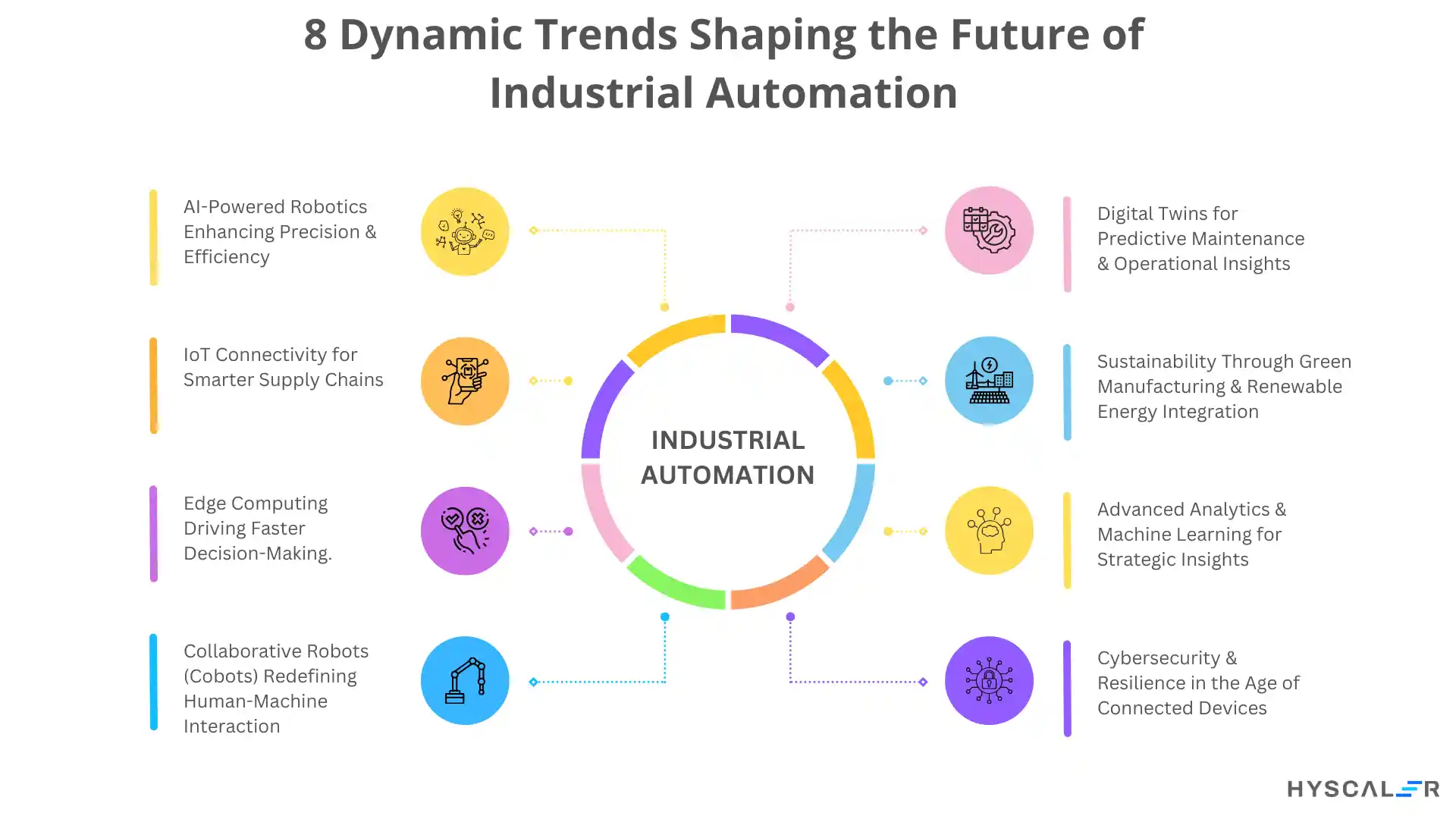
Final Thoughts: Embracing the Future of Industrial Automation
The industry of industrial automation constantly progresses along with technological innovations and new trends that are changing the industrial sector across the world. These trends are critical because companies are looking to stay efficient, innovative, and agile in competitive environments.
An investigation by The Capgemini Research Institute found that 53% of companies expect industrial automation to mitigate workplace accidents, ensure work-process optimization, and advance leaner supply chains. Adaptation to industrial automation trends demands strategic planning, technology spending, and organizational flexibility. Sectors that keep pace with such developments and incorporate them into their day-to-day activities will shape the landscape for sustained success and innovation.
The road to a completely automated world is an invitation for all sectors of the world to take action. As technological opportunity lies just around the corner and consumer demand evolves, it is time for organizations to step up and propel the change and innovation. The future is smart, efficient, and powered by automation— are you ready to lead the way?